Application, process flow and characteristics of cut to length line
Release time:
Sep 04,2024
Description of the use of cut to length line:
Adopting PLC and full hydraulic control, aluminum and aluminum alloy strips are cut into plates of fixed length according to requirements and stacked neatly. Length setting, single machine adjustment and full line automatic operation control are all concentrated on the console.
Production process of cut to length line:
The coil transport trolley transports the aluminum coil to the uncoiler, starts the uncoiler centering cylinder to clamp the aluminum coil; starts the guide plate lifting hydraulic cylinder to lift the guide plate, starts the guide plate elastic hydraulic cylinder to open the aluminum coil; starts the uncoiler to drive the aluminum coil to rotate, so that the aluminum plate successfully passes through the guide plate extension channel and enters the already started pinch roller device, and uses friction to make the aluminum plate pass through the straightening roller device, cleaning device (cleaning oil stains and aluminum powder on both sides of the aluminum plate), multi-roller straightening machine ( eliminating the plate shape defects of the strip ), rotary and translation shears ( servo sizing system for precise cutting), belt conveyor (to check and transport aluminum plates), and enter the stacking table . After reaching the set number of pieces, they are removed to the collection table for subsequent packaging processing.
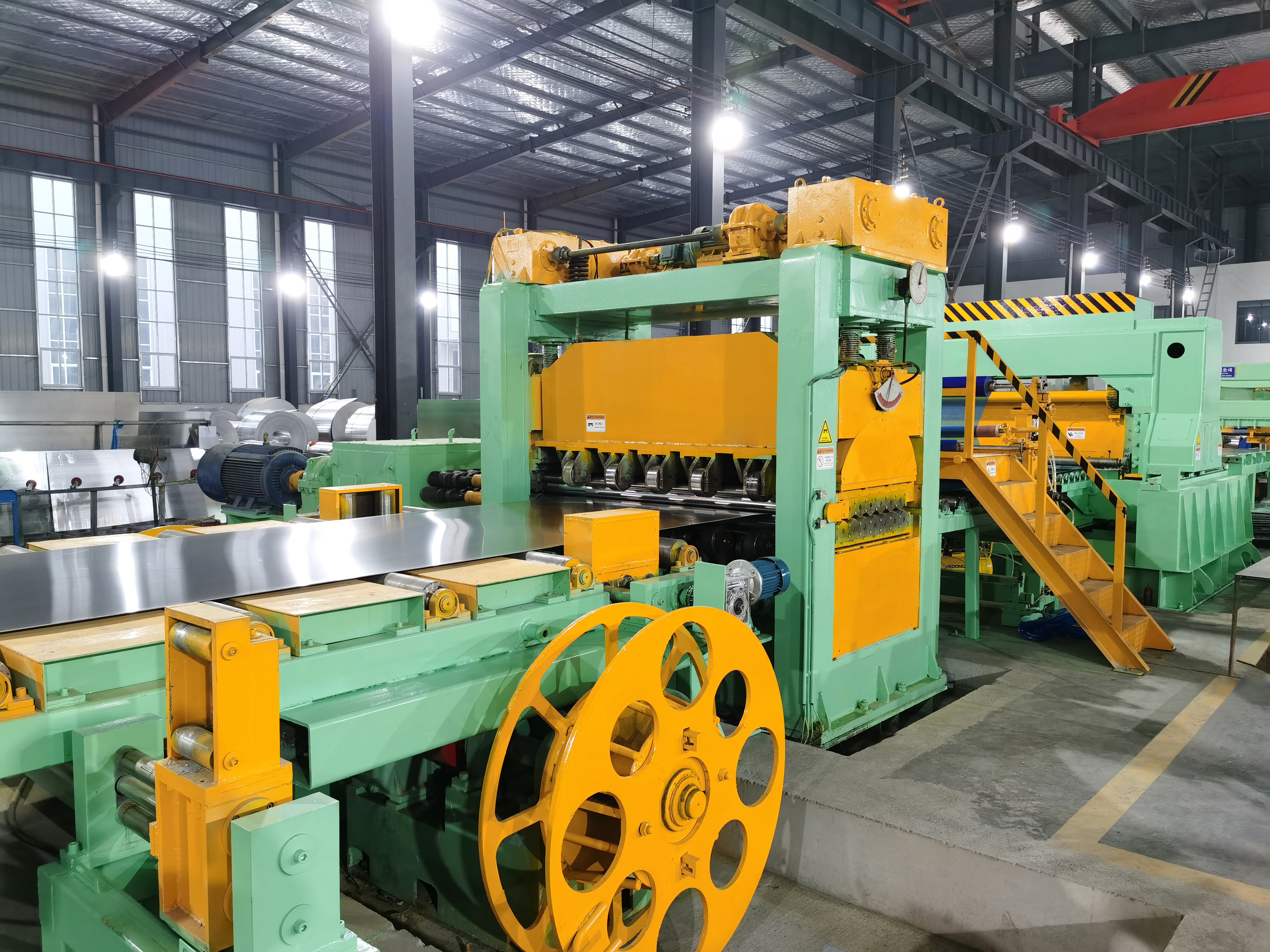
Main features of cut to length line:
1.Cutting method: rotary cutting
The gears used for the transmission of the unit are made of special alloy steel materials . After heat treatment, the gears are ground on imported grinders to safely eliminate the impact noise during shearing . The main drive motor uses a servo motor dedicated to cross-cutting. The length is controlled by a specially designed integrated module, and the length accuracy can reach ±0.5 mm .
2.Straightening equipment: Multi-roller straightening machine
Since the original curvature of the strip changes along the length direction, increasing the number of straightening rollers can improve the straightening accuracy ; by changing the deflection of the working rolls, plate defects such as mid-waves can be eliminated ; by tilting the upper roller system, a small deformation straightening solution can be achieved to reduce the residual stress inside the strip .
3.Adopt no-loop control to reduce scratches, ensure quality and save construction costs.
4.The air cushion type stacking board is used for the stacking board, which can achieve scratch-free and regular stacking board.
Tel:
E-mail:
Address:
Economic Development Zone , Gongyi, China.
Message
Copyright © Zhengzhou Hengzhong Heavy Industry Machinery Manufacturing Co., Ltd.
Powered by :www.300.cn Supported IPV6 Privacy Agreement
COOKIES
Our website uses cookies and similar technologies to personalize the advertising shown to you and to help you get the best experience on our website. For more information, see our Privacy & Cookie Policy
COOKIES
Our website uses cookies and similar technologies to personalize the advertising shown to you and to help you get the best experience on our website. For more information, see our Privacy & Cookie Policy
These cookies are necessary for basic functions such as payment. Standard cookies cannot be turned off and do not store any of your information.
These cookies collect information, such as how many people are using our site or which pages are popular, to help us improve the customer experience. Turning these cookies off will mean we can't collect information to improve your experience.
These cookies enable the website to provide enhanced functionality and personalization. They may be set by us or by third-party providers whose services we have added to our pages. If you do not allow these cookies, some or all of these services may not function properly.
These cookies help us understand what you are interested in so that we can show you relevant advertising on other websites. Turning these cookies off will mean we are unable to show you any personalized advertising.
SAF Coolest v1.3 设置面板 PVDSD-ZFUA-BAXAE-ZQQ
无数据提示
Sorry, there is no content in the current section!
You can view other columns or return to Home